5-axis laser engraving (surface texturing processing, micro-engraving)
5-axis laser engraving (surface texturing processing, micro-engraving)
We offer short-pulse laser engraving on molds.
We can offer a wide range of decorating proposals for primary processing molds, such as injection molding and secondary processing molds such as hot stamping.
We have experience in the fields of automobile interiors and cosmetic containers.
Achievements: Plastic injection molding dies (jar containers for automobile interiors, compacts), direct blow molding dies, injection blow molding dies, plastic heat press molds, plates for hot stamping, plates for embossing
Sibo processing
Feature 1-Reduction of environmental impact
Dramatically reduces environmental impact compared to conventional etching-based graining.
Feature 2-Improved designability
More designable designs and textures can be reproduced on the mold by taking advantage of the laser's microfabrication capability. Complex gradations, multiple heights, and gentle bumps can be expressed. Different expressions such as complex hairlines, gradients, and relief shapes, which cannot be expressed by etching or engraving, can be processed simultaneously. We can also handle complex molds such as curved surfaces. With our in-house design department, we can create fine and unprecedented textures and grains by making full use of our unique know-how. We will assist you in realizing your design by interviewing you based on actual samples and rough sketches of your image.
Feature 3 - Digitalization of the machining process
We can shorten the lead time and guarantee the same quality for multiple-cavity molds, renewal molds, etc.
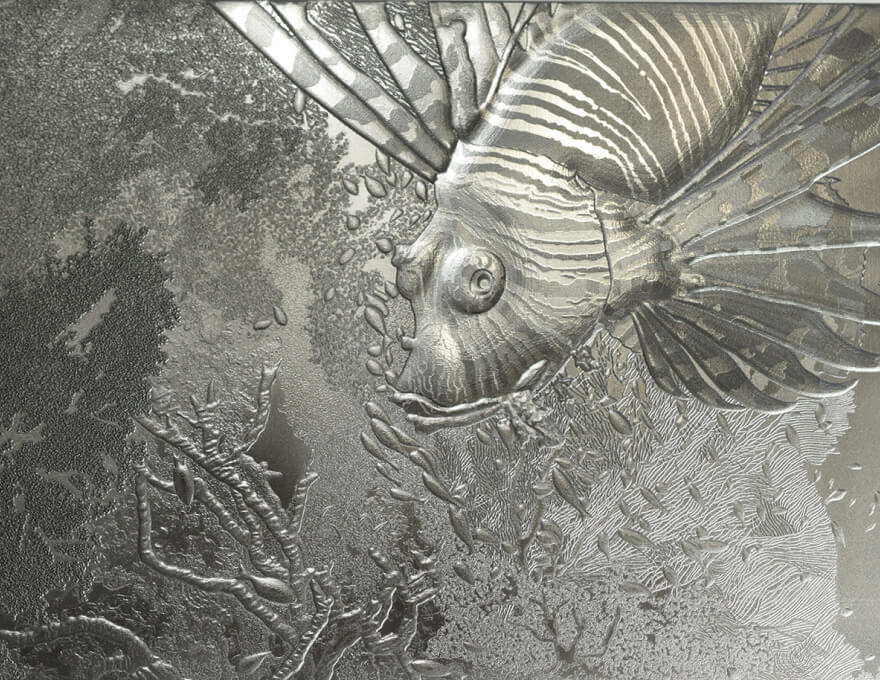
Micro machining
Laser engraving can also be used for engraving fine letters and logos with sharp edges, which are conventionally processed with small-diameter tools and electric discharge.
Comparison with cutting
Sharper edges can be achieved more easily with laser engraving than with conventional small-diameter tools, and there is no risk of tool loss due to steel hardness or engraving depth because the process is not physical like cutting.
Comparison with electric discharge machining
No electrode fabrication process is required as with electric discharge machining, and the process can be performed as a direct engraving on the mold, thus reducing the number of man-hours required for fabrication.
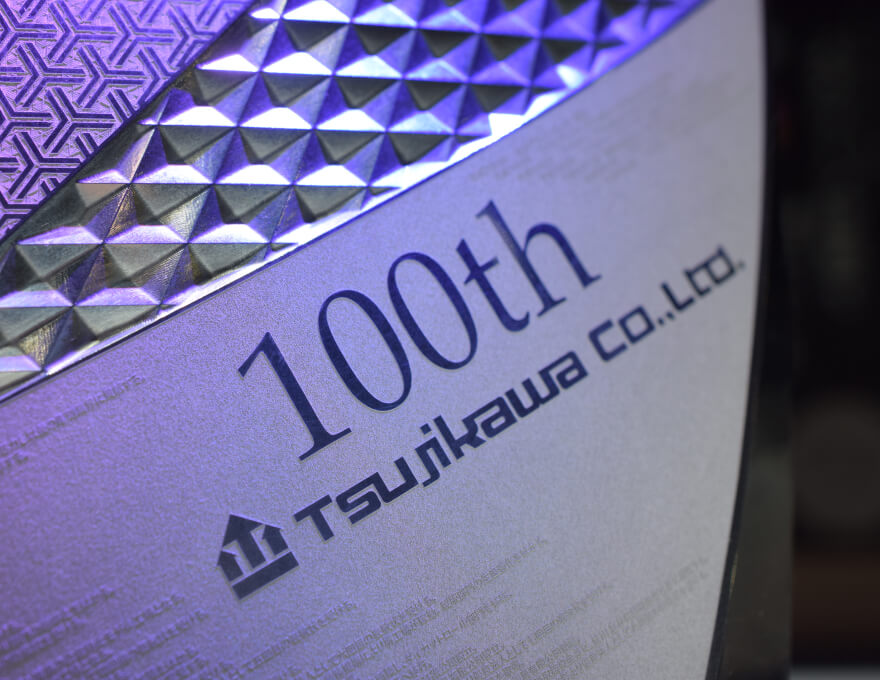